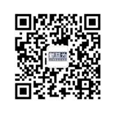
微信公眾號二維碼
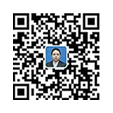
微信咨詢顧問二維碼
新益為精益生產(chǎn)咨詢公司概述:精益生產(chǎn)(Lean Production)又稱精良生產(chǎn),其中“精”表示精良、精確、精美;“益”表示利益、效益等等。精益生產(chǎn)就是及時制造,消滅故障,消除一切浪費,向零缺陷、零庫存進軍。精益生產(chǎn)是從豐田生產(chǎn)方式中總結提煉的先進的管理理念它的核心思想是通過消除企業(yè)所有環(huán)節(jié)上的不增值活動,達到降低成本、縮短生產(chǎn)周期和改善質量的目的。那推行精益生產(chǎn)的基本認知是什么呢?
精益生產(chǎn)咨詢
針對致力于推行精益生產(chǎn)的企業(yè)來講,推行精益首先需要破除思維障礙,熟知推進精益生產(chǎn)的套路,然后再進行頂層設計,這樣才能保證精益生產(chǎn)對企業(yè)百利而無一害。
推進精益生產(chǎn)首先要樹立如下幾個基本認知觀:
一、改善是基于需求而產(chǎn)生的
1、改善的目的要明確,目標要清晰。
目的明確大家清楚為什么要這樣干,目標明確了,努力的方向也就確定了。
2、設定改善評價指標。
評價指標要界定清楚,便于項目成員的努力能有效地進行衡量;
3、改善要基于現(xiàn)地現(xiàn)物。
改善需要明確問題,問題需要描述清楚,切忌宏觀大論;
二、改善需求全員參與
1、盡可能多的讓作業(yè)的人共同參與。改善是圍繞現(xiàn)地現(xiàn)物所進行,故每天作業(yè)的人員盡可能多地參與改善活動,可以起到現(xiàn)身說法的作用。
2、全員的范圍很廣泛:既包括管理決策層,也包括中基實施層,更涵括作業(yè)操作層;不少企業(yè)在推進精益時,始終認為精益=生產(chǎn),一直認為是生產(chǎn)部門的事;更有人認為精益是實施項目組的事,與其他人員無關。不理解全員參與的概念,在實施過程中就很難統(tǒng)一認知,一旦遇到障礙,就會形成“你們”與“我們”兩個特別清晰的立場。
三、精益不僅要做能做的事情,還要向不能做的事情發(fā)起挑戰(zhàn)
改善不能基于表象的改善,更要深入挖掘表象內的真象。表象通常容易做,不少人也喜歡去做,但精益要求的不僅僅是做表象的改善,還要通過表象的改善與探秘,對影響企業(yè)的真正的頑固問題發(fā)起挑戰(zhàn),從而改變企業(yè)對真象的認知。精益是通過挑戰(zhàn)來認識真象的,也是通過挑戰(zhàn),讓企業(yè)成員充分認識“能”與“不能”、“行”與“不行”認知的。
四、做設備改善之前先做作業(yè)改善
不少企業(yè)害怕改善,其實是害怕花錢。這是企業(yè)對改善認知不足有關,也與個別咨詢人員的咨詢閱歷有關。精益要求改善的邏輯遵循先作業(yè)改善,然后再進行設備改善。
理由有以下三點:
其一:設備改善需要花錢,作業(yè)改善不需要花錢;
其二:作業(yè)改善后再進行有目的性的設備改善,花少錢即可完成,而且又可以避免重復改善。
其三:如果沒有進行徹底的作業(yè)改善,就盲目導入自動化,其實就是在浪費內置于自動化中了,也就是俗稱的浪費自動化。
五、徹底追求真實的原因:5why分析法
1、 5why分析法,不是問人,而是要去問物。對于缺乏走動習慣的企業(yè)領導層來說,更多的是問人,而不是問物,故真實的原因往往難以找到。即便找到了,也只是翻譯過的表象。
2、對于結果或期望沒有達到預期的時候,要善于尋找真正的原因。不少企業(yè)在推進精益改善項目時,在不同階段均會表達出不滿意。但對這些不滿意,很少進行過認真檢討,探究真實原因,故也始終無法獲得改善的真諦。
六、策略決定后首先要確認安全與品質
任何改善策略的制定均是在確保安全與品質的前提下進行的。改善的目的是讓作業(yè)更安全,品質更穩(wěn)定,而違背此目標的改善均是不合格的。
七、想到了就馬上要行動
1、不能判定時可以先嘗試。一時之念不一定正確,但如果不嘗試,就連驗證的機會也沒有了。改善需要鼓勵嘗試,鼓勵嘗試其實就是鼓勵行動,容許成員有條件地“犯錯誤”。
2、巧遲不如拙速。如果只有60分,就立即行動,這是改善的真諦。真諦理解容易,但實施起來卻困難重重,因為擁有審批權限的人,“巧遲”與“拙速”他們通常選擇前者。
推行精益生產(chǎn)的基本認知是什么?以上就是新益為精益生產(chǎn)咨詢公司的相關介紹,做好企業(yè)的精益生產(chǎn)管理工作就是為精益生產(chǎn)管理活動打下基礎,讓精益生產(chǎn)管理在企業(yè)中發(fā)展有一個良好的前提。
建立生產(chǎn)有序、管理順暢,操作規(guī)范,士氣高昂、高質量、低成本、短交期的作業(yè)現(xiàn)場;
為企業(yè)規(guī)劃設計一套由內到外的形象升級,外觀視覺價值體現(xiàn)、內在的管理內涵體現(xiàn);
全員參與設備管理高產(chǎn)出和低成本運營,提升設備管理能力,維護能力,提高效率
構建班組生產(chǎn)管理體系、循環(huán)評價、人才育成、持續(xù)改善、績效管理、文化養(yǎng)成體系;
提高產(chǎn)品質量、降低生產(chǎn)成本、縮短交期、增加利潤,讓管理更系統(tǒng)科學,執(zhí)行力更強
對工廠的各個組成部分進行合理安排,以提高生產(chǎn)效率、降低成本、優(yōu)化物流、改善工作環(huán)境等