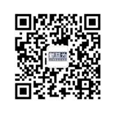
微信公眾號二維碼
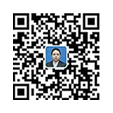
微信咨詢顧問二維碼
新益為5S咨詢公司概述:精益生產(chǎn)認為所有這種快速發(fā)貨和計劃安排的活動,都是在浪費時間、人力和金錢。龐大的、雜亂無序的和緩慢搬運的緩沖庫存,也被精益生產(chǎn)視為浪費。因為額外的活動和多余的庫存,使產(chǎn)品增加了時間和費用,必須把它們消滅掉。
精益生產(chǎn)的管理方法克服了這些不平衡問題。精益生產(chǎn)的管理方法是一種唯一可供采用的操作系統(tǒng),這種系統(tǒng)僅僅利用必要的資源,就可以滿足顧客的需求,從而達到了平衡。為滿足顧客需求的資源利用的理想水平,可以用來表明現(xiàn)有資源沒有達到最佳化的程度。由于這個原因,精益生產(chǎn)的管理方法在大多數(shù)的情況下,會同資源消耗的當前度量系統(tǒng)發(fā)生沖突。
精益生產(chǎn)方法
精益生產(chǎn)線是先進的生產(chǎn)線,某工廠布置可使企業(yè)采用順序漸進的方式來完成標準的工作任務。在可能的情況下,制造產(chǎn)品必要的全部工序,實際上都連接在一起。資源裝備的這種實際連接,可以使工作任務在整個生產(chǎn)周期中,得到均勻分配、聚集和平衡。在“賣出”一個工件時,整條生產(chǎn)線就會把第二個工件“一步-步地推向”下游。精益生產(chǎn)線被設計得可使全部工序都以同一速度進行工作。因為產(chǎn)品是每次一件以同一速度生產(chǎn)出來的,所以這種類型的生產(chǎn)線,往往被歸類為“ 流動”生產(chǎn)線。
精益管理方法在可用生產(chǎn)能力的利用方面,與MRP的模式大不相同。精益生產(chǎn)的管理方法,規(guī)劃了所需未來的生產(chǎn)能力,計算了每一道 工序的資源裝備,并且安排了企業(yè)的這些資源裝備放置得互相靠近。因為所有資源裝備,都以相同的速度進行工作,并且在它們的消耗點處實際上連接在一起, 所以就沒有必要把工作合成批量或組合起來,來達到每個工段的效率和利用率。把顧客的每日需求編成順序列表是必要的,但是MRP發(fā)出的車間指令,對于安排精益生產(chǎn)線各工序的計劃來說,就不再需要了。精益生產(chǎn)的管理方法,首先集中在生產(chǎn)工序之間達到平衡,而達到工段的效率、利用率和消耗率的必要性,則成為次要目標。
在規(guī)定的SOE的人時和機時,完全被分成等于節(jié)拍時間的情況下,精益生產(chǎn)的管理方法,是一種生產(chǎn)線平衡技術(shù)。
把生產(chǎn)工序加以平衡到節(jié)拍時間,并且實際加以連接起來,就可以使得一個工序的產(chǎn)出,直接被另一個工序消耗掉。這就令人驚異地減少了庫存和生產(chǎn)過程時間。因為生產(chǎn)工序已完全分成相等的工作組成部分,所以再沒有必要把相似的人力和機器組成“工段”了。只有生產(chǎn)需求量的所需資源裝備,才放置在生產(chǎn)線上。
在不再受到不平衡工段規(guī)則限制的情況下,在制品緩沖庫存的庫房已不容許再存放工件了。生產(chǎn)工序一旦達到平衡并且連接在一 起進行順序生產(chǎn)之后,產(chǎn)品就可以接近于它們實際加工量的時間來生產(chǎn)。每一次只有一個工件步步地被推動通過所有工序,并且每經(jīng)過一個節(jié)拍時間, 只有一個工件被推離生產(chǎn)線的終點。在通過不同的批量生產(chǎn)工段的產(chǎn)品正常流程中所需的等候和排隊時間,就被大大地縮減或消除掉了。
節(jié)拍時間是一種時間/產(chǎn)量關(guān)系。 它是由進行加工可用的時間,被每一道工序所要求的產(chǎn)量相除計算出來的。節(jié)拍確定了一道工序要達到設計產(chǎn)出量必須的運行速度。
精益生產(chǎn)的目標是要建立和設計-條 能夠順序生產(chǎn)多產(chǎn)品的生產(chǎn)線,每次一件地通過必需的工序來生產(chǎn)產(chǎn)品。精益生產(chǎn)線能夠只利用實際制造產(chǎn)品所需的時間量,來實現(xiàn)這個目標。通過產(chǎn)品各種不同的生產(chǎn)工序,來生產(chǎn)產(chǎn)品所需的實際加工時間,幾乎總是要比批量產(chǎn)品通過工廠的流程所需的時間要短。精益生產(chǎn)消除了非增值的等候時間,并減少了計劃安排和排隊的時間。
精益生產(chǎn)的管理方法可以使產(chǎn)品-次 一件地按規(guī)定的速度生產(chǎn)出來, 沒有等候時間、排隊時間或其他延誤。產(chǎn)品利用來自下游-道工序的信號,被拉動通過生產(chǎn)線,而同按指令指揮的計劃系統(tǒng)被推動相反。由于沒有顧客需求而制作產(chǎn)品所耗費的時間,被認為是“非增值”時間。精益生產(chǎn)的管理方法消除了非增值時間。
建立生產(chǎn)有序、管理順暢,操作規(guī)范,士氣高昂、高質(zhì)量、低成本、短交期的作業(yè)現(xiàn)場;
為企業(yè)規(guī)劃設計一套由內(nèi)到外的形象升級,外觀視覺價值體現(xiàn)、內(nèi)在的管理內(nèi)涵體現(xiàn);
全員參與設備管理高產(chǎn)出和低成本運營,提升設備管理能力,維護能力,提高效率
構(gòu)建班組生產(chǎn)管理體系、循環(huán)評價、人才育成、持續(xù)改善、績效管理、文化養(yǎng)成體系;
提高產(chǎn)品質(zhì)量、降低生產(chǎn)成本、縮短交期、增加利潤,讓管理更系統(tǒng)科學,執(zhí)行力更強
對工廠的各個組成部分進行合理安排,以提高生產(chǎn)效率、降低成本、優(yōu)化物流、改善工作環(huán)境等